1. Ma Juan Guodian Suzhou Second Thermal Power Co., Ltd., Suzhou, Anhui 234000; 2. Wei Xuan Xi'an Thermal Engineering Research Institute Co., Ltd., Xi'an, Shaanxi 710054; 3. Cao Feng, Xuzhou Yike Electric Co., Ltd., Xuzhou, Jiangsu 221000
Abstract: This article analyzes the error sources of traditional electronic belt scales and introduces the system composition and performance characteristics of high-precision intelligent control matrix electronic belt scales, based on the transformation practice of a certain thermal power plant's incoming coal electronic belt scale. The experimental results confirm that the high-precision intelligent control matrix electronic belt scale can meet the requirements of 0 The use requirements of the Level 2 belt scale and the ability to maintain long-term stability.
Keywords: Belt scale transformation, error source, high-precision intelligent control matrix, 0 Level 2 belt scale, long-term stability
Reference code: A
Article number: 1002-1183 (2021) 04-0008-05
1. Current situation of coal management in Fossil fuel power station
As the consumable energy of Fossil fuel power station, coal directly determines the production and operation costs, energy consumption indicators, profit margins and overall business performance of the power plant. From incoming sampling, dumper, coal stacking, coal taking, coal blending, to furnace metering, coal feeder distribution and metering, each link of the overall process needs to be linked, in place and mutually dependent. In recent years, the fuel control efforts and requirements of various power generation groups have been elevated to unprecedented new heights. The equipment department, power generation department, fuel department, and even plant leaders need to put a lot of effort into paying attention to and ensuring the safe, reliable, stable, and accurate operation of relevant equipment.
Precise weighing, metering and calorific value analysis are required for coal entering the plant, which is the general gate for external settlement of Fossil fuel power station. The use of precise weighing and measuring equipment mainly includes three aspects: (1) the actual operation of weighing and measuring accuracy; (2) Stable period of accuracy within the allowable range; (3) Cost control of human, material, and financial resources for later maintenance. This is the key pain point of Fossil fuel power station at present, and also the core problem to be solved, which directly affects cost control and business performance assessment. The measurement of the incoming coal belt scale, which is necessary for each power plant, is related to the cost accounting of coal consumption and calorific value, and its accuracy and stability are crucial. However, the measurement deviation of traditional belt weigher is large and the stability is very poor, which brings huge maintenance to the thermal control department. Frequent calibration can not solve the problem at all, which has become the key problem that most Fossil fuel power station need to solve.
This article explores the use of high-precision intelligent control matrix belt weighers to achieve 0 A feasible solution for level 2 measurement accuracy.
2. Background of Belt Scale Transformation
A certain thermal power plant's coal feeding conveyor belt # 12A/B is equipped with one fully suspended belt scale with four rollers and four sensors for each belt, which serves as the basis for calculating the coal feeding into the power plant and is equipped with a cyclic chain code verification device. The belt scale has low accuracy and poor stability, and conducting a cyclic chain code verification once a week cannot guarantee precise use
Figure 1 Schematic diagram of belt scale
According to the force analysis, the following conclusion can be obtained: FC=FW-2FP · sin α (1)
In order to detect the true weight of the material, we hope that 2FP · sin in the equation α The item is zero or a constant.
Figure 2 Force Analysis Diagram
FP - Belt tension; FW - The force to be measured (after deducting the sum of the weight of the scale frame and belt, it is the weight of the conveyed material); FC - force acting on the sensor; α— The angle formed between the belt tension FP and the horizontal direction after the weighing roller is forced to sink.
In equation (1), as follows: α = 0, then 2FP · sin α The item is zero. To achieve α = 0, which requires the belt scale to ensure that the upper surface of the weighing roller and the fixed roller are in the same plane.
Therefore, to improve the accuracy of the belt scale, it is necessary to control it in various aspects such as manufacturing, installation, and daily maintenance.
Firstly, in the manufacturing process, high requirements are put forward for the concentricity of the rollers, as well as the height and surface condition of the upper surface of the rollers. Usually, it is required that the radial runout of the roller during manufacturing should not exceed 0 2 mm; Adjust the height difference on the upper surface of the roller during installation to not exceed 0 5mm, during use, it is necessary to regularly clean the scale frame and inspect, replace the supporting rollers, etc.
α Another important reason for the occurrence of the problem is that the weighing frame sinks after the belt is loaded, so improving the stiffness of the weighing frame and reducing load sinking has become one of the main means to improve the accuracy of the belt scale. The result is that The belt scale has become very bulky (usually weighing hundreds of kilograms). On the contrary, the bulky scale body inevitably experiences small displacement of the support points and force points due to support reasons during the operation of the belt, which greatly affects the long-term stability of the belt scale.
Installation is also an important factor affecting the accuracy of belt scales. Usually, the installation specifications and actual installation work of belt scales raise the requirement that the weighing roller and fixed roller of the belt scale should be adjusted on the same plane as the upper surface. Some domestic enterprises use laser collimators for calibration during installation. However, the collimation obtained through such careful adjustment will no longer exist during use due to reasons such as deformation of the scale frame load and welding stress release deformation; Moreover, due to material contamination and wear of the supporting rollers, the weighing roller and fixed roller of the belt scale cannot be kept in the same plane for a long time. That is to say, in practical use α The value cannot be zero or a constant.
The FP in the error term is the belt tension, which is a fundamental attribute of belt conveying. It will vary with changes in belt speed, material flow rate, and the tightness, softness, and hardness of the belt; The hardness of the belt will vary with changes in temperature and humidity. Obviously, the belt tension cannot be constant, such an uncertain force and a variable α The angle constitutes a 2FP · sin that the belt scale cannot overcome and cannot maintain constant α This error term seriously affects the measurement accuracy and long-term stability of the belt scale. Most users of belt scales are well aware of the many influencing factors that they cannot eliminate. What can achieve is to maintain the accuracy of the belt scale through strengthened maintenance and continuous calibration.
4. Implementation of high-precision belt scale transformation
According to the current GB/T 7721-2017 continuous cumulative automatic weighing instrument, as well as JJG 19
Table 1 Main Technical Parameters of Belt Conveyor
1) Pre renovation situation
Before the renovation, the physical verification results of the two # 12A/B belt scales are shown in Table 2, and the weighing of the actual coal is carried out using a truck scale.
Table 2 Physical verification results before renovation
From the data in Table 2, it can be found that the short-term repeatability and stability of traditional belt scales are poor, and the medium to long-term stability is even more unsatisfactory. The data from the simulated load test using cyclic chain codes before the renovation is shown in Table 3.
Table 3 Cyclic Chain Code Verification Results
From Table 3, it can be seen that the simulated load test results using cyclic chain codes do not meet the requirements of 0 Level 5 indicator requirements can only meet Level 2 indicator requirements.
2) Situation after renovation
After the renovation, the physical verification results of two intelligent control matrix type belt scales for # 12A/B are shown in Table 4.
Table 4 Physical verification results after renovation
From Table 4, it can be seen that the physical verification results using the intelligent control matrix belt scale meet the requirements of 0 Level 2 indicator requirements. At the same time, a 3-month stability assessment was conducted on the # 12A/B two intelligent control matrix belt scales with an interval of 1 month. The stability results are shown in Table 5.
Table 5 Stability Data
The data of simulated load test using hanging code after transformation is shown in Table 6.
Table 6 Hanging Code Verification Results
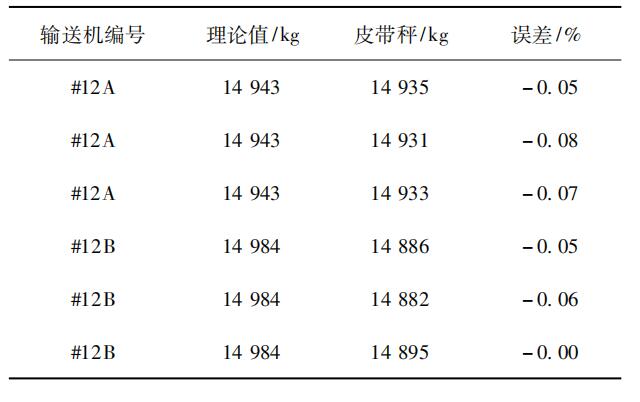
From Table 6, it can be seen that after the transformation, the accuracy of using hanging codes is significantly improved compared to the original cyclic chain code verification. Conclusion 6: The renovation practice has confirmed that high-precision intelligent control matrix electronic belt weighers can meet the requirements of 0 The use requirements of Level 2 high-precision belt scale and long-term stability. The self calibration technology has a unique algorithm and a high degree of intelligence, which can achieve automatic calibration and accuracy correction under normal coal conveying operation of the conveyor. This completely changes the way traditional belt scales are maintained, achieving maintenance free. The widespread application of high-precision intelligent control matrix belt scale technology has fundamentally improved the measurement problems of conveyors in the power generation industry, as well as in industries such as steel, cement, and coal mines.
Reference:
Xu Xinrong Research on a new type of electronic belt weigher [ D ]. Xi'an: Northwestern Polytechnical University, 2002.
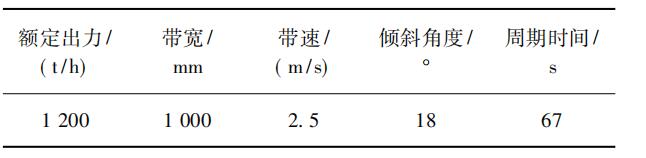
JJG 195– 2019 Continuous Accumulated Automatic Scale (Belt Scale) [S].
GB 7721– 2017 Continuous Accumulated Automatic Weighing Scale (Belt Scale) [S].
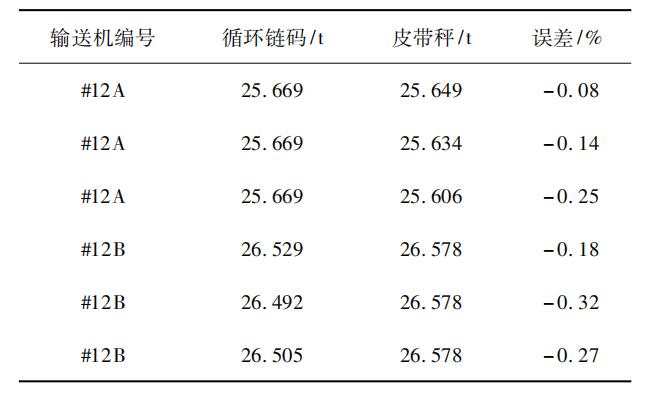
Hao Pengyu Design of a New Distributed Electronic Belt Scale [ J ]. Mining and Metallurgy, 2016 (4): 64.
Cao Feng High precision belt scale: 208296949U [P]. 2018-12-28.
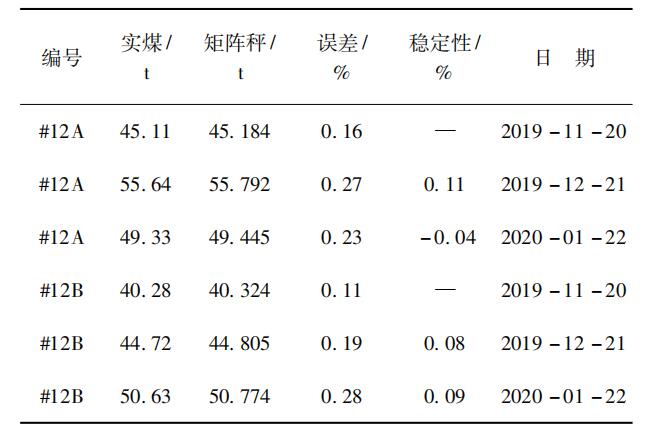
Quan Qidong An automatic hanging code verification device for electronic belt scales: 208296969U [P]. 2018-12-28
Systematic modeling and analysis of uncertainty component and uncertainty calculation method of tube coefficient are carried out, and the influencing factors of uncertainty of Pitot tube coefficient calibration are discussed in combination with test data. It is proved that under the condition that the test equipment is determined, the value of combined standard uncertainty of Pitot tube coefficient calibration decreases with the decrease of Pitot tube coefficient value and the increase of linearity, The expanded uncertainty decreases with the increase of the decimal places of the Pitot tube coefficient< Br/> Reference:
Hu Lintao, Wang Yi Research on calibration method of Pitot tube [ J ]. Measurement Technology, 2018 (z1): 85.
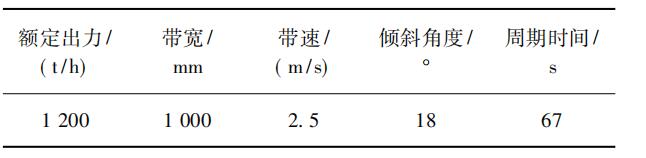
JJG 518&flash; 1998 Pitot tube Verification Regulation [S].
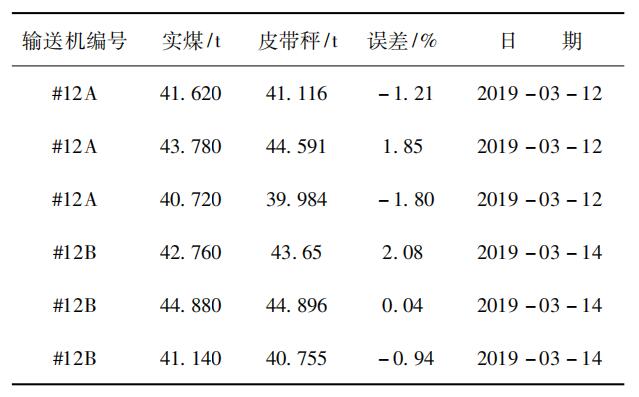
JJG 99&flash; 2006 Weight Verification Regulations [S].
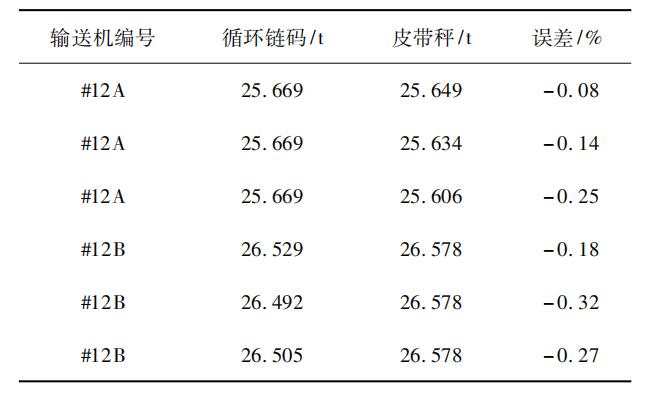
JJF 1059 1– Evaluation and Representation of Measurement Uncertainty in 2012 [S].
GBT 27418– 2017 Measurement uncertainty Evaluation and Representation [S]